06.01.2020
5 minutes de lecture
Future constraints on pollutant emissions pushed car manufacturers towards Direct-Injection Spark-Ignition (DI-SI) technologies to improve engine performances and reduce both fuel consumption and emissions. New challenges are then introduced in terms of combustion optimization, due to a more complex phenomenology and a larger number of degrees of freedom, while system models require developments to approach such new engine architectures with the sufficient level of detail.
A combustion model that works toward a more comprehensive approach
In order to achieve the latter objective, a PhD work performed at IFPEN[1] hosted the development and validation of a Zero-Dimensional (0D) model of DI-SI combustion for system simulation. The proposed model focuses on physics of atomization and drop evaporation, fuel/air mixing, flame propagation in heterogeneous charge and mutual interaction between these phenomena, Figure 1.
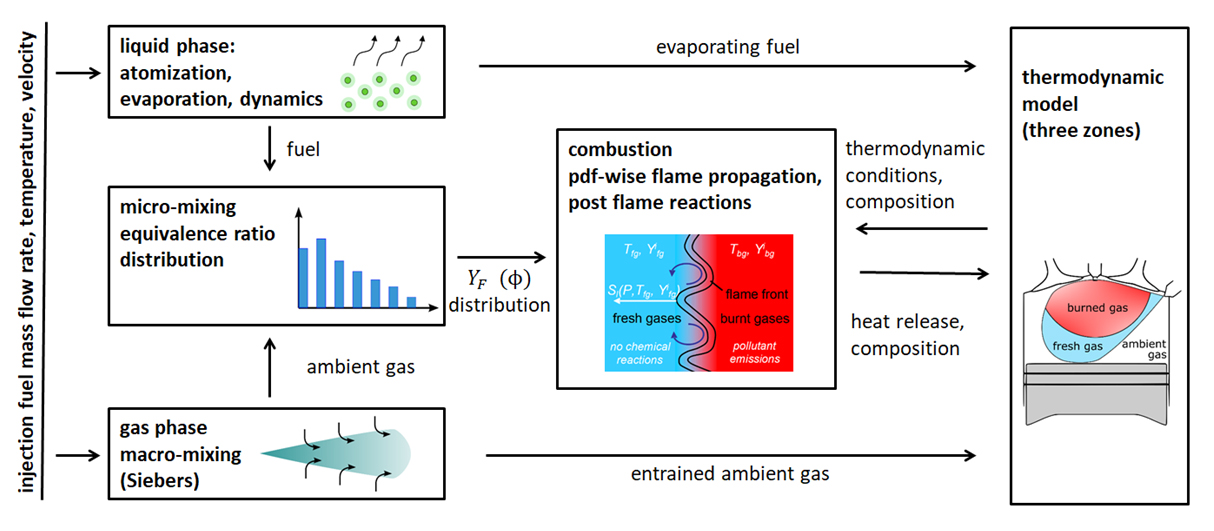
In particular, it is characterized by the following aspects:
- The liquid phase is discretized in parcels grouping drops of the same size. An empirical atomization model based on injection velocity, fuel characteristics and thermodynamic conditions provides initial diameters. A Lagrangian model including drag-inertia dynamics, heat-up and forced convection describes drop parcel penetration and evaporation.
- Fuel / air mixing is described using a discrete Probability Density Function (PDF) approach, based on constant-mixture-fraction classes interacting with each other and with the drop parcels[2].
- Flame propagation takes into account mixture heterogeneity effects on flame speed and pollutant production is modeled.
A validation method based on experimental results and simulation tests
The approach was validated against experimental results, when available, and 3D CFD* RANS** simulations[3], Figure 2 and Figure 3.
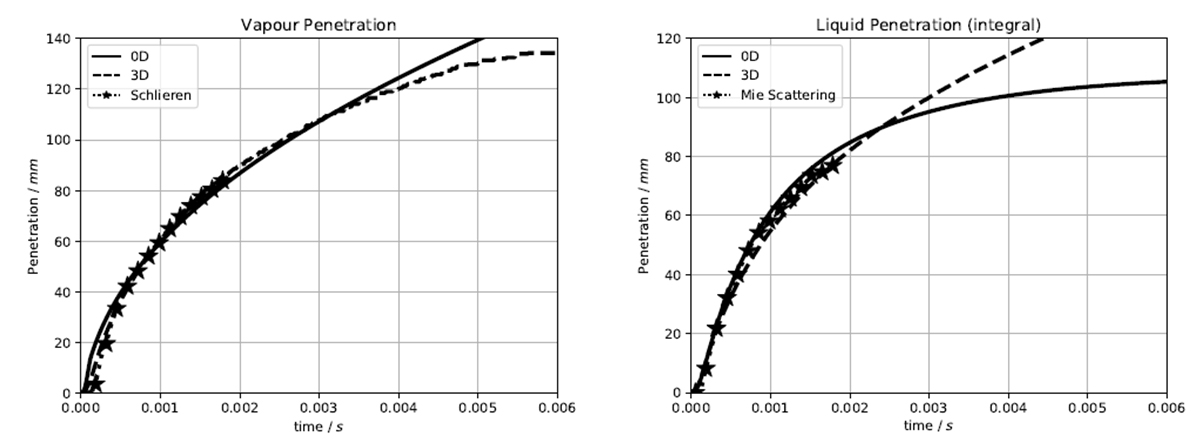
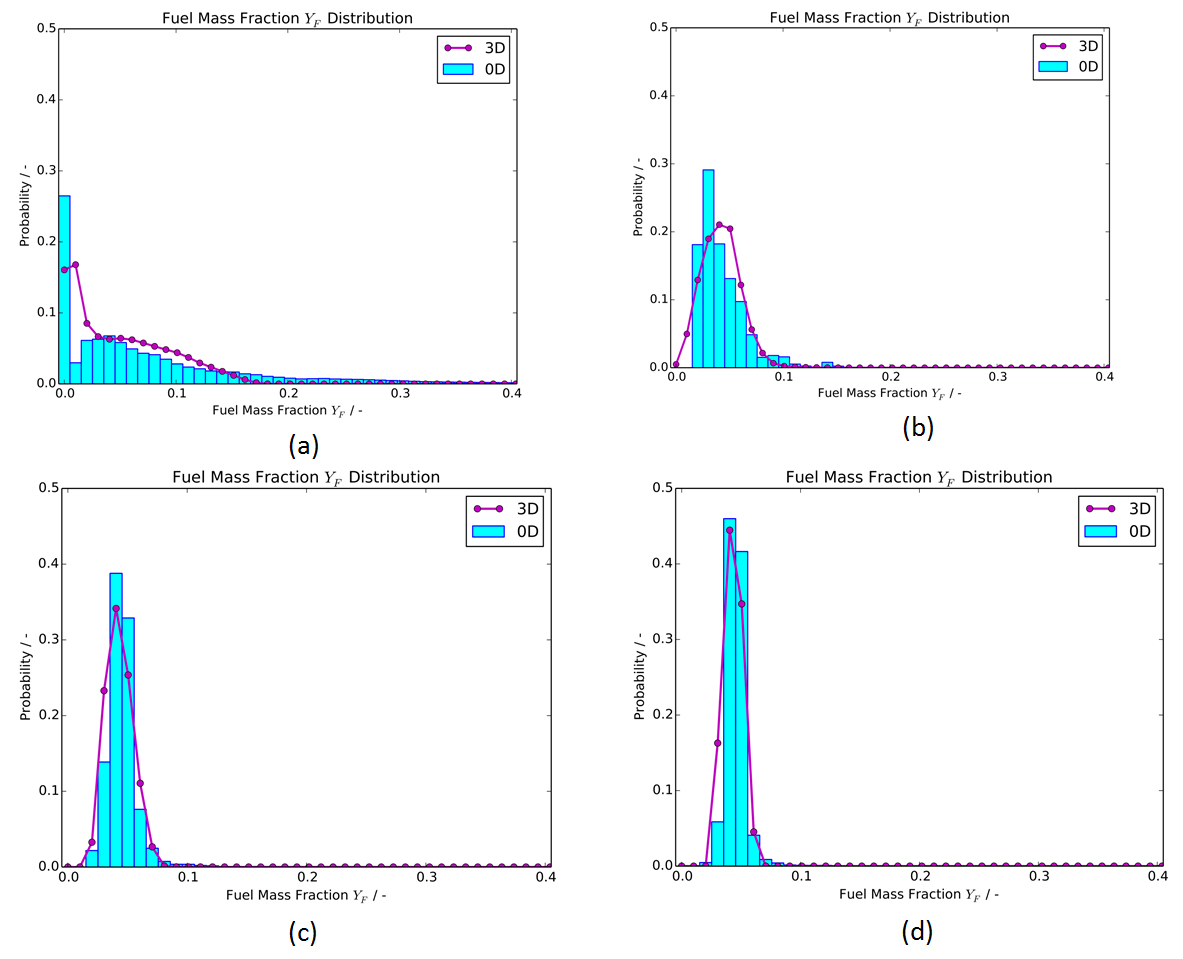
* CFD = Computational Fluid Dynamics
** RANS = Reynolds-Averaged Navier–Stokes
*** 270 CAD = Crank Angle Degree
**** BTDC = Before Top Dead Center
The implemented model already opens up multiple perspectives
The model was implemented in the Simcenter Amesim platform for multi-physical modelling of the Siemens Digital Industries Software and integrated in the CFM Spark Ignition combustion chamber submodel of the IFP-Engine library.
This PhD work opens various perspectives for future works:
- The discrete PDF, only applied so far to the fresh mixture, could be employed to describe the mixing-controlled post-oxidation reactions in the exhaust gas, thus improving the gaseous pollutant emissions prediction capability of the model;
- The parcel-based liquid phase model could be used to predict the mass of liquid fuel colliding with the cylinder walls, information that can be used to develop a liquid film model;
- Predicting mass and drops size of liquid fuel present in the cylinder during combustion is also highly relevant in the context of soot formation modelling.
Scientific Contact: Alessio Dulbecco
Publications
[1] F. Pellegrino, System Simulation of Combustion in Direct-Injection Spark-Ignition Engines, CentraleSupelec PhD thesis, 2019.
[2] F. Pellegrino, A. Dulbecco, D. Veynante, Development of a Quasi-Dimensional Spray Evaporation and Mixture Formation Model for Direct-Injection Spark-Ignition Engines, SAE Technical paper, 2015
>> DOI: 10.4271/2015-24-2471
[3] F. Pellegrino, A. Dulbecco, D. Veynante, Development and validation of a quasi-dimensional spray model for DI-SI engines, Thiesel conference on Thermo-and-Fluid Dynamic Processes in Direct Injection Engines, poster session, 2018.