Témoignage de Li Zhang, ingénieur process à IFPEN
D’après le scénario NZE (Net Zero Emission) de l’IEAa, le déploiement du CCUS (Carbon Capture Utilisation and Storage) doit s’accélérer pour passer d’environ 40 Mt de CO2 captées au niveau mondial en 2022 à 1 Gt en 2030 [1]. Parmi les solutions développées, le captage en postcombustion au moyen de solvants est, à ce jour, considéré comme l’une des plus robustes, efficaces et pertinentes [2].
C’est ainsi qu’est née la solution DMXTM, qui répond au besoin de disposer de technologies efficaces et économiques. Fruit de plus de 10 ans de recherche à IFPEN, cette technologie arrivant en phase finale de développement, avait besoin d’être démontrée dans un cadre industriel réel [3] [4].
Aussi, en 2019, le projet 3Db (DMX Demonstration in Dunkirk) a vu le jour, avec comme objectif de construire un démonstrateur industriel. Pour ce faire, quoi de mieux que de le construire dans un des plus grands sites industriels d’Europe, participant ainsi à la feuille de route de décarbonation d’un des principaux émetteurs français, le site sidérurgique d’ArcelorMittal à Dunkerque (photo 1) ?
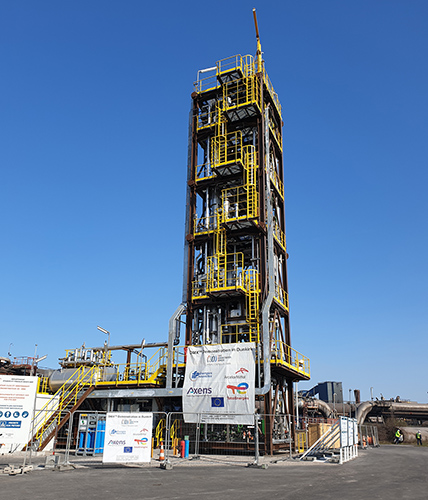
Ce projet a nécessité la contribution d’une équipe spécifique d’IFPEN implantée sur le site industriel, pour suivre la construction et réaliser les tests, avec le soutien à distance de l’équipe IFPEN basée sur le site de Solaize. Pour la première fois, IFPEN avait la responsabilité d’une opération sur un site industriel extérieur !
Les modules de plus de 26 mètres de hauteur sont arrivés sur site en novembre 2021, après des mois d’études et de construction en atelier.
Après raccordement du démonstrateur aux conduites des gaz de haut fourneau du site sidérurgique, les opérations de mise en route des équipements ont démarré en mars 2022 sous la coordination technique du partenaire AXENS (photo 2).
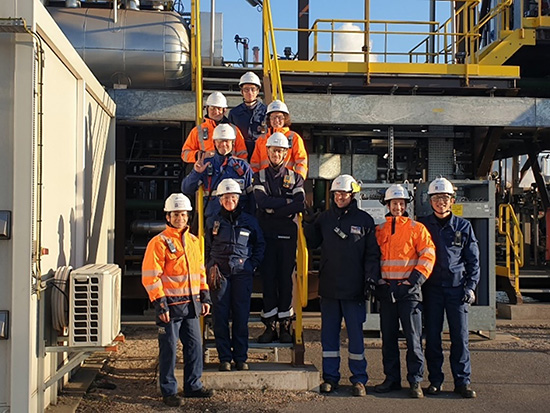
En tant qu’ingénieur process au sein de l’équipe IFPEN, j’ai suivi les essais depuis la mise en route jusqu’à la fin de la campagne de tests sur le site de Dunkerque. Avant de m’y rendre, j’avais travaillé en tant qu’ingénieur « Process Design », en utilisant une première version du simulateur numérique du procédé DMXTM. Cette fois, je me trouvais « de l’autre côté », pour participer à l’acquisition des données expérimentales qui ont permis d’améliorer le modèle de simulation, lequel servira à dimensionner les futurs équipements !
Je me suis aussi confronté à la réalité du terrain et à tous les imprévus qui peuvent survenir pendant une démonstration et qui rendent chaque point expérimental unique et précieux. La démonstration industrielle et la conception des procédés sont ainsi les deux faces d’une même pièce !
A ce jour, un peu plus de 2 ans après la fin de la construction sur site, la démonstration du procédé DMXTM est terminée. Après évaluation sur des compositions de gaz représentatives de différentes applicationsc (aciérie, cimenterie ou centrale électrique), les performances du procédé de captage ont été validées, révélant divers bénéfices :
- une réduction particulièrement intéressante de la pénalité énergétique (30 % de moins par rapport à des solvants de type MEA ou CESAR1d),
- une capacité de captage importante du solvant, une haute qualité du CO2 captée,
- une bonne stabilité du solvant, etc.
Au-delà du succès de la démonstration, les données obtenues lors de la campagne de tests ont permis de produire une nouvelle version du simulateur dont va bénéficier le partenaire AXENSf.
Même si la démonstration du procédé DMXTM est aujourd’hui terminée, l’équipement de Dunkerque va encore être utilisé quelques mois pour tester une nouvelle formulation de solvant. Cette fois-ci, je suivrai les tests depuis mon poste à IFPEN mais ce sera l’opportunité pour d’autres collègues d’aller vivre cette expérience unique : celle de voir aboutir concrètement des années de recherche au service de la décarbonation de l’industrie et ainsi contribuer à la lutte contre le dérèglement climatique.
a- International Energy Agency (Agence Internationale de l’énergie AIE).
b- Les partenaires du projet : ArcelorMittal France, TotalEnergies et AXENS. Capacité du démonstrateur : 0.5t CO2 capté par heure.
c- Le gaz haut fourneau a servi comme base du gaz de charge pour l’unité, mais d’autres compositions ont été produites volontairement avec les recyclages de l’unité, afin de valider le procédé DMXTM pour de différentes applications.
d- MEA : solution aqueuse avec monoethanolamine, CESAR1 : solution aqueuse avec 2-amino-2-methylpropanol (AMP) and pipérazine (PZ).
e- Pureté du CO2 supérieure à 99 % (CO2 sec).
f- Développement du logiciel piloté par P. Bachaud et V. Carlier.
Références :
-
IEA Ed.
>> https://www.iea.org/reports/world-energy-outlook-2023
-
L. Raynal, P.A. Bouillon, A. Gomez, P. Broutin, From MEA to demixing solvents and future steps, a roadmap for lowering the cost of post-combustion carbon capture, Chemical Engineering Journal 171 (2011) 742-752.
>> DOI: 10.1016/j.cej.2011.01.008
-
P. Broutin, P. Briot, S. Ehlers, A. Kather, Benchmarking of the DMXTM CO2 Capture Process, Energy Procedia 114 (2017) 2561-2572.
>> DOI: 10.1016/j.egypro.2017.03.1414
-
M. Dreillard, P. Broutin, P. Briot, T. Huard, A. Lettat, Application of the DMXTM CO2 Capture Process in Steel Industry, Energy Procedia 114 (2017) 2573 -2589.
>> DOI: 10.1016/j.egypro.2017.03.1415
Contact scientifique : catherine.laroche@ifpen.fr Cheffe de projet : Vania Moreau