27.03.2025
3 minutes de lecture
Soumises à des sollicitations en service de plus en plus fortes, les nouvelles machines électriques pour la mobilité voient leurs conducteurs et leurs isolants exposés à des risques croissants de dégradation. Pour le suivi du vieillissement des bobinages, IFPEN propose une nouvelle stratégie, en ligne et sans matériel dédié, de caractérisation fréquentielle d’impédance.
Les inconvénients des méthodes actuelles
Avec l’arrivée de nouveaux composants d’électronique de puissance, toujours plus rapides et performants, la tendance pour les groupes motopropulseurs de traction électrique est à l’augmentation des fréquences de découpage1 et des tensions d’alimentation [1]. Les conducteurs des machines électriques et leurs isolants sont de ce fait soumis à des contraintes électriques de plus en plus fortes, avec des risques de dégradations accrues. Afin de préserver ces systèmes, et ainsi réduire les coûts et les temps de maintenance, il est aujourd’hui indispensable de suivre l’évolution de leur état de santé. Pour cela, des stratégies de mesure des décharges partielles [2], de mesure des résistances d’isolement [3] ou d’estimation des capacités inter-spires [4] peuvent être mises en place. Leur coût, leur mise en œuvre hors-ligne ou leur difficulté d’intégration de série dans un véhicule sont les principaux inconvénients de ces méthodes. Pour répondre à la problématique posée, IFPEN propose une nouvelle stratégie, en ligne et sans matériel dédié, de caractérisation fréquentielle d’impédance, pour le suivi de vieillissement de bobinages.
1 Fréquence à laquelle les interrupteurs de puissance commutent d’un état passant à un état ouvert
Une caractérisation simplifiée et réalisable en fonctionnement
Traditionnellement, la mesure d’impédance est réalisée sur une machine à l’arrêt et déconnectée de sa source de puissance via un analyseur d’impédance. D’autres approches, hors-ligne ou par systèmes de couplage, consistent à exciter le bobinage à l’aide d’impulsions de tension à fréquence donnée afin de reconstruire le diagramme de Bode2 de cette impédance [5]. L’inconvénient majeur de ces méthodes est leur caractère invasif3, et la nécessité de disposer de systèmes d’excitation/caractérisation dédiés.
La solution développée à IFPEN permet de s’affranchir du système d’excitation dédié, tout en permettant une caractérisation d’impédance à chaque instant, lorsque le moteur est en fonctionnement. L’idée proposée consiste à utiliser l’excitation harmonique des bobinages, liée à l’alimentation via un onduleur de tension [6], afin de caractériser le comportement fréquentiel de ces derniers, au moyen des seules mesures de courant et de tension aux bornes de la machine.
2 Représentation en fréquence de la réponse d'un système
3 Méthodes qui affectent le fonctionnement de la machine
Principe d’identification du comportement fréquentiel des bobinages
Le processus de caractérisation consiste d’abord à mesurer les tensions aux bornes du moteur, ainsi que le courant qui circule dans chacune de ses phases (Figure 1(a)). Une analyse fréquentielle de ces signaux est alors réalisée (Figure 1(b)). On cherche ensuite les composantes fréquentielles dont l’amplitude est supérieure à un seuil fixé4. Puis, pour chacune de ces fréquences prépondérantes, on calcule l’impédance à l’aide de la loi d’Ohm (Figure 1(c)).
4 Seuil dont le comportement s’apparente à l’inverse de la fréquence
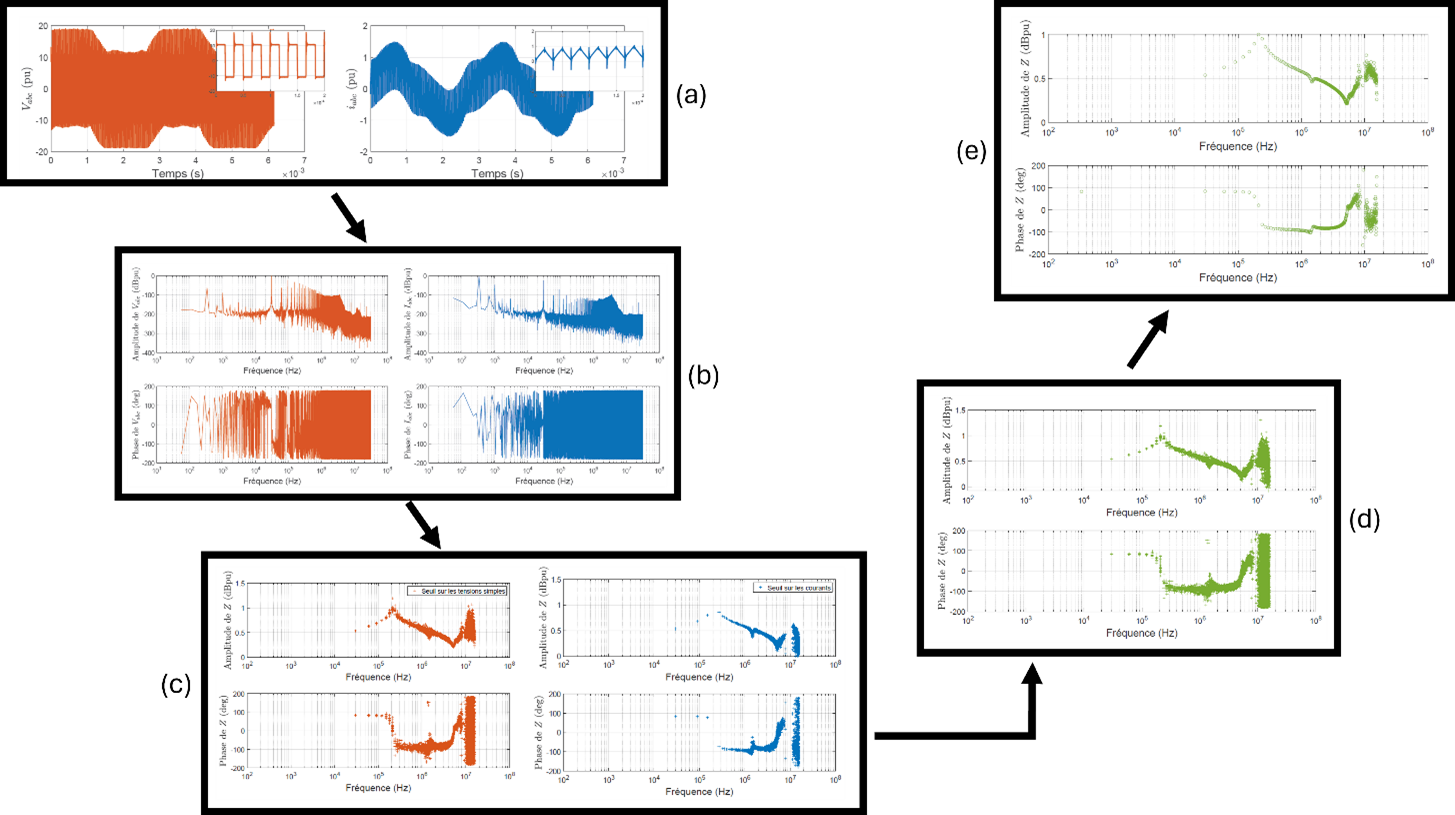
L’étape suivante consiste simplement à concaténer les caractéristiques d’impédance brutes issues des seuillages sur les tensions et sur les courants (Figure 1(d)). Enfin, les données sont nettoyées, afin de ne garder que les fréquences autour des multiples de la fréquence de découpage, qui sont les seules réellement excitées (Figure 1(e)).
Une approche aux avantages multiples
L’intérêt de la méthode proposée tient aux points suivants :
- L’excitation harmonique étant naturellement réalisée via l’onduleur de tension, la méthode n’impacte pas le fonctionnement de la machine, ni son vieillissement.
- Aucun câble de mesure ou adaptateur de fixation n’est nécessaire, ce qui dispense d’une phase de calibration préalable, rendant ainsi la mesure d’impédance d’autant plus fiable.
- Le suivi de vieillissement est réalisé à tout instant et sans retirer la machine de son environnement fonctionnel, ce qui rend possible l’identification précoce d’une dégradation d’isolation dans les bobinages.
Application à la maintenance préventive des machines électriques
Il a été montré que l’évolution du diagramme de Bode de l’impédance des bobinages de machines électriques est directement liée à l’état de santé des isolants [7,8]. En effet, la première fréquence de résonance parallèle est directement liée à la capacité inter-spires, et donc à la qualité d’isolation des bobinages. Grâce à l’évaluation précise de cette résonance, tout au long du fonctionnement du moteur, la méthode proposée permettra de suivre l’évolution de l’état de santé des bobinages. Dans une stratégie de maintenance conditionnelle5, un tel suivi pourra par conséquent être utilisé afin d’estimer la durée de vie restante du bobinage (RUL6), et ainsi pouvoir garantir les meilleures performances et le meilleur taux de disponibilité du système.
5 Forme de maintenance préventive subordonnée à l'état de l'équipement
6 Remaining Useful Life
Références :
[1] Bose B. (2020). Power Electronics And Motor Drives - Advances and trends. Academic Press (éd. 2). ISBN : 9780128213605
[2] Kaufhold M., Borner G., Eberhardt M., & Speck J. (1996). Failure mechanism of the interturn insulation of low voltage electric machines fed by pulse-controlled inverters. IEEE Electrical Insulation Magazine, 12(5), 9–16.
>> https://doi.org/10.1109/57.537190
[3] Stone G. C. (2005). Partial discharge diagnostics and electrical equipment insulation
condition assessment. IEEE Transactions on Dielectrics and Electrical Insulation, 12(5), 891–903.
>> https://doi.org/10.1109/TDEI.2005.1522184
[4] Werynski P. (2006). Vieillissement des diélectriques et surveillance in situ des machines électriques. Thèse de doctorat, LSEE, Université d’Artois. En ligne :
>> https://www.researchgate.net/publication/272857976
[5] Creux J., Haje Obeid N., Boileau T., & Meibody-Tabar F. (2024). Online high frequency impedance identification method of inverter-fed electrical machines for stator health monitoring. Applied Sciences, 14(23), 10911.
>> https://doi.org/10.3390/app142310911
[6] Chen W., Sun H., Gu X., & Xia C. (2016). Synchronized space-vector PWM for three-level VSI with lower harmonic distortion and switching frequency. IEEE Transactions on Power Electronics, 31(9), 6428–6441.
>> https://doi.org/10.1109/TPEL.2015.2499774
[7] Haje Obeid N. (2016). Contribution à la détection des défauts statoriques des actionneurs à aimants permanents - Application à la détection d’un défaut inter-spires intermittent et au suivi de vieillissement. Thèse de doctorat, GREEN, Université de Lorraine. En ligne : >> >> >> https://tel.archives-ouvertes.fr/tel-01530619/
[8] Perisse F., Mercier D., Lefevre E., & Roger D. (2009). Robust diagnostics of stator insulation based on high frequency resonances measurements. IEEE Transactions on Dielectrics and Electrical Insulation, 16(5), 1496–1502.
>> https://doi.org/10.1109/TDEI.2009.5293965
Contacts scientifiques : Jérémy Creux, Najla Haje Obeid
Vous serez aussi intéressé par
Machines électriques et aimants recyclables : des technologies de pointe pour économiser la matière
Machines électriques : conception, optimisation, contrôle et diagnostic
Comme tous les secteurs concernés par l’électrification, celui du transport nécessite la conception de systèmes électriques performants et efficaces qui répondent à de multiples contraintes, telles que le coût et la compacité. Dans ce contexte, l’optimisation est devenue une étape primordiale du processus de conception de ces systèmes, en particulier pour les machines électriques...
L’électronique de puissance au cœur des enjeux de la mobilité électrique
Dans le cas des véhicules électrifiés, à batterie (électriques ou hybrides) ou à pile à combustible (PAC), les convertisseurs d’électronique de puissance (EdP) jouent un rôle majeur car ils y sont utilisés pour différentes fonctions. Ils servent par exemple à piloter des moteurs électriques, à gérer l’énergie à bord du véhicule ou à contrôler la recharge de la batterie de traction...